Polystyrene Beads for Insulation In My Home?
- The Energy Efficiency Group
- Sep 7, 2022
- 4 min read
Updated: Aug 5, 2023
Polystyrene beads, also known as expandable polystyrene (EPS) beads, are a popular insulation material for insulating cavities, but they also come with some major concerns. We will discuss here what you need to be aware of when considering EPS for cavity wall insulation.
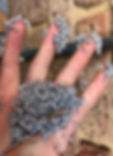
1. It has failed to meet compliance with the Victorian Building Authority failing the combustibility fire spread test results.
2. Outlined by BRANZ It's not recommended for use in New Zealand due to its reaction with electrical cable sheathing. We will summarise both the VBA and BRANZ findings below.
The Fire Risk: One of the main risks associated with polystyrene bead insulation is the potential for fire. EPS beads are made from a flammable polystyrene plastic and if exposed to an ignition source, they can rapidly ignite. Insulation needs to pass common Fire testing performance including the products flame spread, smoke release, and overall combustibility. While many products boast 'fire retardants' they still need to meet a standard. This is because insulation can be an ignition source leading to a dangerous and potentially deadly fire. Additionally, once ignited, insulation like polystyrene EPS beads release a toxic smoke when exposed to flame, which can be hazardous to human health.
The Victorian Building Authority commissioned an independent full-scale fire test report which concluded:
Test Failed: Rendered Expanded Polystyrene (EPS), a form of cladding popular in the building industry due to its lower cost and insulation properties, has failed key fire spread tests conducted by the VBA. This indicates it can result in rapid vertical fire spread and pool fires when exposed to large fire sources, creating a high fire risk in Class 2-9 buildings of Type A or B construction.
Lack of Awareness by the Building Industry: The results are a concern due to the widespread use of EPS in the construction industry, especially since the product's fire behavior is poorly understood by some designers, builders, and building surveyors. Misunderstanding the risk could lead to EPS's continued use in non-compliant ways, increasing public safety risk.
Findings Conclusion: In Victoria, rendered EPS can only be used in Class 2-9 buildings of Type A or B construction if certain stringent conditions are met, including the preparation of a documented performance solution by a registered fire safety engineer, documented evidence complying with Part A5.2 Evidence of Suitability of the BCA, and a determination of the Building Appeals Board.
The Challenge of Future Non-compliance: Non-compliance poses a serious risk to occupant safety and is subject to severe disciplinary action. The cost and difficulty of removing and replacing non-compliant cladding can also be significant, causing additional stress and anxiety to building owners.
Recommendations: Building occupants are advised to seek information on combustible cladding and ensure proper maintenance of the building's Essential Safety Measures (ESMs). Fire safety advice is also provided to mitigate risks.
Final Clarification Notes: The test results are specific to the performance of rendered EPS (with fire retardant) in EIFS on Class 2-9 buildings of Type A and B construction, and not applicable to other classes of buildings or wall system configurations.
Read the full report here: https://www.vba.vic.gov.au/__data/assets/pdf_file/0016/120904/VBA-EPS-Industry-Update.pdf
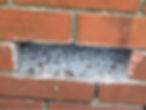
Electrical Cable Deterioration: Outlined by BRANZ EPS Bead Insulation is not recommended for use in New Zealand due to its reaction with electrical cable sheathing. This publication by Adrian Bennett, BRANZ Materials Manager concluded avoiding use of loose-fil EPS beads.

Heat Generation: All electrical cables generate heat when carrying electricity. The amount of heat generated depends on the electrical current and the thickness of the copper conductor. Bundling cables together or surrounding them by insulation can lead to increased heat.
Regulations: The New Zealand Electricity Regulations 1997 ensure that electrical cables used in buildings operate within a set temperature range, taking into account wire size, cable bunching, and building insulation effects.
Plasticiser Migration: The most common sheathing material for cables is PVC, which is often plasticised using phthalate-esters. These plasticisers can migrate out of the PVC under certain conditions, for example, when in contact with polystyrene insulation. This process can lead to the formation of a sticky film on the cable sheathing and the "eating into" of the polystyrene by the cable.
Risk of Short Circuit: If the PVC sheathing loses enough plasticiser, it can become brittle. If the cable is then flexed, this could potentially lead to a short circuit between the wires in the core.
Preventative Measures: The risks associated with PVC cables in contact with polystyrene insulation can be mitigated by using cables with migration-resistant plasticisers or preventing direct contact between the cables and the polystyrene. Other strategies include maintaining cable temperatures at lower levels and wrapping the cable with tape or ducting.
Precaution Checklist: Recommendations for safer cable usage include supporting horizontal cabling, fixing vertical cabling, avoiding loose-fill EPS beads as insulation, using the correct cable size for the load and anticipated temperature, and considering the use of migration-resistant cabling or special electrical design to control cable temperatures..
Read full report here: https://www.buildmagazine.org.nz/assets/PDF/BUILD65-26-ElecCableInPoly.pdf
Another risk associated with polystyrene bead insulation is its impact on the environment. EPS beads are made from fossil fuels, meaning their production contributes to greenhouse gas emissions and as EPS beads are not biodegradable, they can take hundreds of years to decompose.
In summary, polystyrene bead insulation may be effective in insulating homes but its flammability, risk of eroding electrical cables, environmental impact and potential negative impact on indoor air quality make it a material that should be used with caution.
It may be worthwhile to consider alternative insulation material for Cavity Wall Insulation like BCA approved an CodeMark Certified Supafil blow in wall insulation. .
Disclaimer: The views and opinions expressed in this blog post are those of the author(s) and do not necessarily reflect the official policy or position of any other agency, organization, employer, or company. The information provided in this post is for general informational purposes only and should not be construed as professional or expert advice. Readers are encouraged to conduct their own research and consult with a professional in the relevant field for any specific concerns or queries.
Author: Cameron. H